What is Automated Quality Management: System, Control & Automation
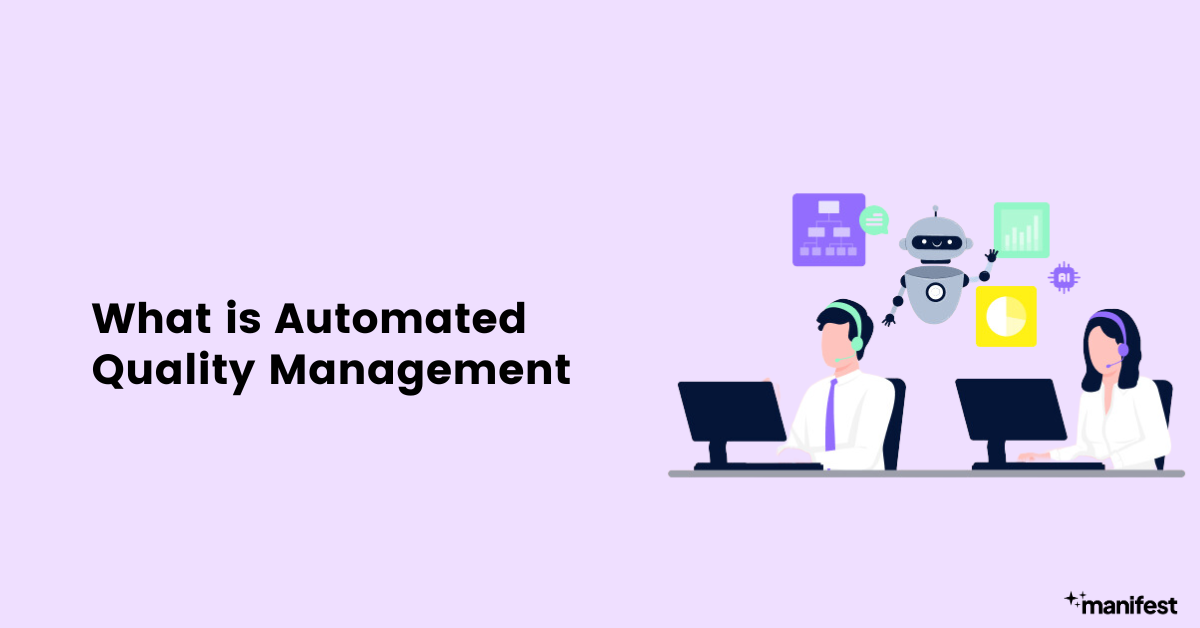
Quality management has always been a cornerstone of successful business operations. With advancements in technology, the integration of automated systems has revolutionized the way quality is managed, controlled, and ensured. Automated Quality Management (AQM) leverages advanced software and hardware solutions to streamline quality processes, ensuring higher efficiency and accuracy.
What is Automated Quality Management?

Automated Quality Management refers to the use of advanced technologies to manage and control quality processes automatically. This encompasses a range of activities from inspection to compliance, ensuring that every aspect of production or service delivery meets predetermined standards.
Components of Automated Quality Management
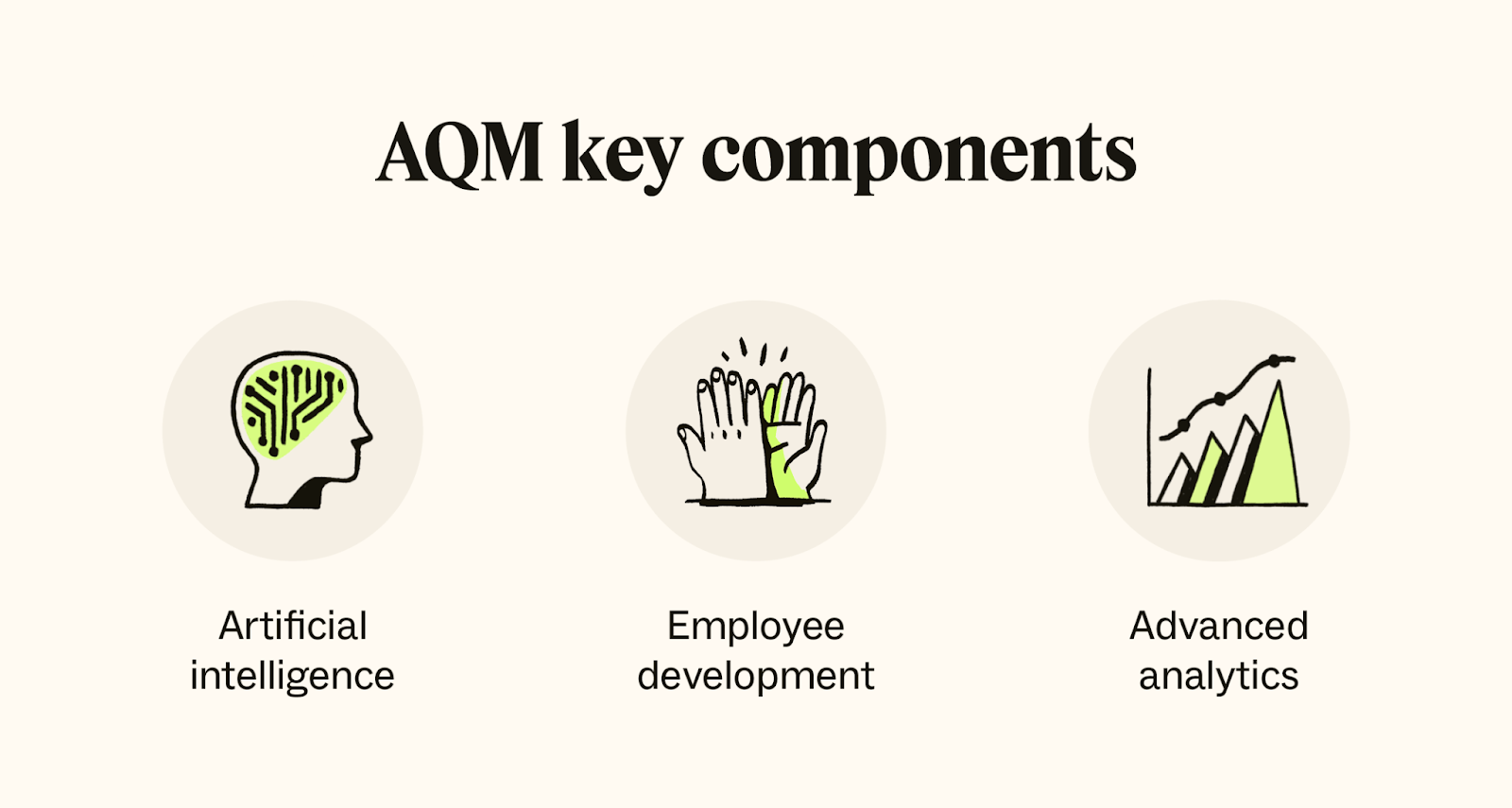
Here are the components of an automated quality management system:
Quality Management System (QMS)
A Quality Management System is a formalized system that documents processes, procedures, and responsibilities for achieving quality policies and objectives. QMS helps coordinate and direct an organization’s activities to meet customer and regulatory requirements.
Control Mechanisms
Control mechanisms in AQM involve tools and techniques to monitor and control quality. These mechanisms ensure that quality processes are followed and standards are met consistently.
Automation Technologies
Automation in quality management includes the use of software and hardware to perform tasks that would otherwise require human intervention. This includes data collection, analysis, and reporting.
Benefits of Automated Quality Management
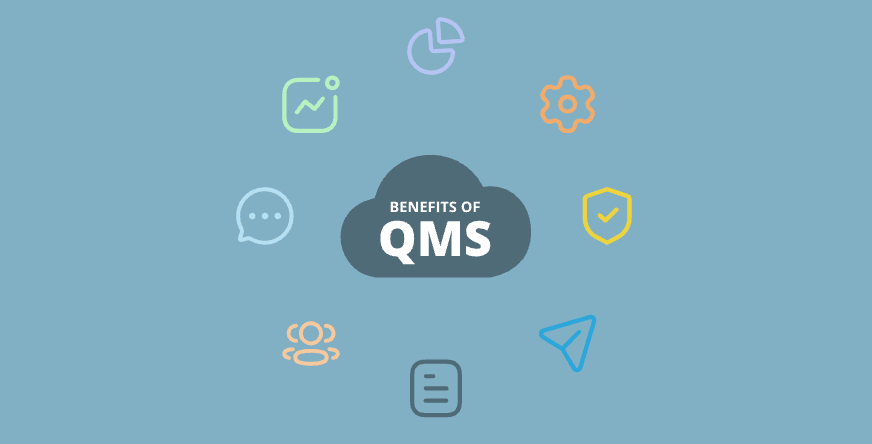
Automated Quality Management Systems (AQMS) offer numerous benefits that enhance overall business operations and product quality.
Consistency and Accuracy
Automation minimizes human error, ensuring that processes adhere strictly to set standards. This consistency results in uniform product quality, which builds customer trust and reduces the likelihood of defects or recalls.
Efficiency and Speed
Automated systems handle repetitive and complex tasks much faster than human workers. This efficiency not only speeds up production but also frees up human resources for more strategic activities. The result is a significant reduction in operational costs and an increase in throughput.
Compliance and Reporting
Maintaining compliance with industry regulations is crucial for avoiding legal issues and fines. AQMS facilitates this by automatically generating detailed reports and documentation required for audits. This ensures that all processes are transparent and traceable, making it easier to prove adherence to regulatory standards.
Types of Quality Management Systems
Quality management systems (QMS) are structured frameworks used to manage and improve the quality of products and services. There are various types, each with distinct features and methods.
Traditional Quality Management Systems
Traditional quality management systems often involve manual processes. These include:
- Paper-based Documentation: Quality procedures and records are maintained in physical files. This method can be cumbersome and prone to errors.
- Manual Inspections: Quality checks are performed by human inspectors. While this allows for detailed examination, it is time-consuming and inconsistent.
- Static Reporting: Reports are generated manually, often resulting in delayed data that may not reflect real-time conditions.
Automated Quality Management Systems
Automated quality management systems use technology to enhance traditional methods. Key aspects include:
- Digital Documentation: Quality documents are stored and managed electronically, ensuring easy access and reducing errors.
- Automated Inspections: Tools and sensors perform quality checks, providing more consistent and accurate results.
- Real-time Reporting: Data is collected and analyzed in real-time, enabling prompt decision-making and corrective actions.
Hybrid Quality Management Systems
A hybrid approach combines elements of both traditional and automated systems. This can be beneficial for organizations transitioning to full automation or those with specific processes that still require manual oversight.
Automated Quality Management Framework
An automated quality management framework consists of several interrelated components that work together to ensure high-quality standards.
Core Components
- Quality Management Software (QMS): Central to the framework, the software facilitates document control, process management, and compliance tracking.
- Sensors and Data Collectors: Hardware devices that monitor production processes and collect data for analysis.
- Integration Tools: Ensure seamless interaction between the QMS and other enterprise systems like ERP (Enterprise Resource Planning) and CRM (Customer Relationship Management).
Key Processes
- Data Collection: Automated systems gather data from various sources in real-time.
- Data Analysis: Advanced analytics tools process the collected data to identify trends and potential issues.
- Automated Reporting: The system generates reports and dashboards for easy visualization of quality metrics.
- Corrective Actions: When issues are detected, the system can trigger predefined corrective actions, ensuring timely resolution.
Challenges in Implementing Automated Quality Management
Implementing an automated quality management system (AQMS) can be challenging. Here are some common issues and how to address them:
Common Issues
- Resistance to Change: Employees may be hesitant to adopt new technologies.
Solution: Provide comprehensive training and involve employees in the implementation process to ease the transition.
- High Initial Costs: The upfront investment in new technology can be substantial.
Solution: Conduct a cost-benefit analysis to demonstrate long-term savings and ROI. Consider phased implementation to spread out costs.
- Integration Complexities: Ensuring the AQMS integrates smoothly with existing systems can be difficult.
Solution: Work with experienced vendors who can provide integration support and ensure compatibility.
- Data Security Concerns: Protecting sensitive quality data is critical.
Solution: Implement robust cybersecurity measures and ensure the AQMS complies with industry standards for data protection.
- Scalability Issues: The system should be able to grow with the organization.
Solution: Choose a flexible AQMS that can scale as your business expands.
How to Choose the Right Quality Management System
Choosing the right quality management system is crucial for maximizing the benefits of automation. Here are some key considerations:
Factors to Consider
- Business Needs: Identify your specific quality management needs and objectives.
Example: If regulatory compliance is a priority, ensure the system includes robust compliance tracking features.
- User-Friendliness: The system should be intuitive and easy to use to encourage adoption.
Example: Look for systems with a straightforward interface and clear documentation.
- Scalability: Ensure the system can scale with your business.
Example: Choose a system that can handle increased data volumes and additional users as your business grows.
- Integration Capabilities: The system should integrate seamlessly with your existing software.
Example: Check for compatibility with your ERP, CRM, and other critical systems.
- Vendor Support: Consider the level of support provided by the vendor.
Example: Opt for vendors who offer comprehensive training, implementation assistance, and ongoing technical support.
Best Practices
- Conduct a Needs Assessment: Thoroughly assess your quality management requirements before selecting a system.
- Pilot Testing: Implement the system on a small scale first to identify potential issues.
- Vendor Evaluation: Research and evaluate multiple vendors to find the best fit for your needs.
- Employee Training: Ensure that employees receive adequate training on the new system to facilitate smooth adoption.
FAQs
How can artificial intelligence enhance quality management?
AI can provide predictive analytics, automate inspections, and reduce human error in quality management processes.
How does automated quality management benefit businesses?
It improves efficiency, accuracy, and compliance, leading to cost savings and better product quality.
What is automation quality control?
Automation quality control refers to the use of technology and automated systems to monitor, analyze, and manage the quality of products or services. This approach reduces human error and increases efficiency by relying on tools and sensors to perform inspections and gather data in real time.